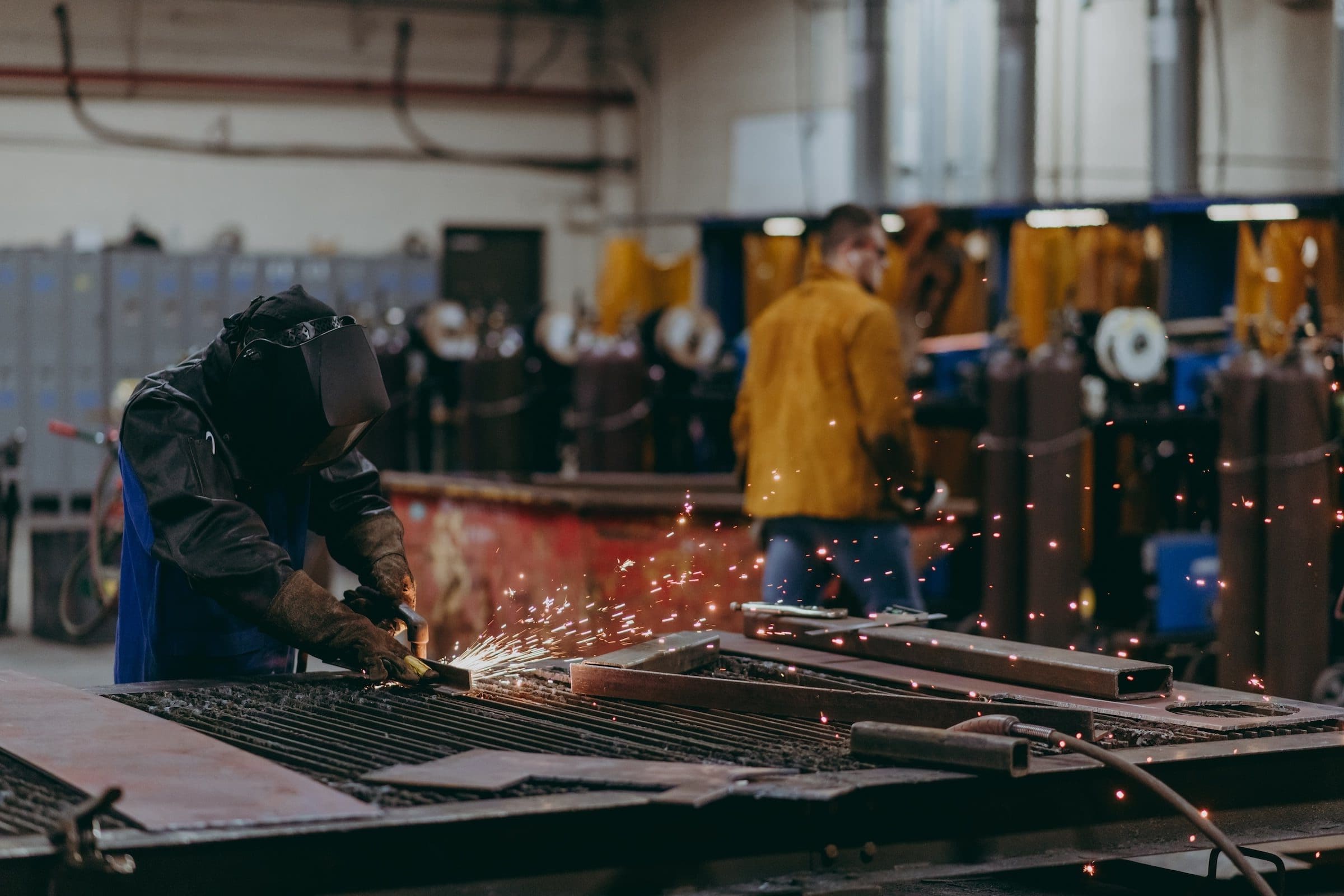
Welding Technology
Get started today
About Welding Technology
The Welding Technology Program provides the opportunity to develop skills necessary to be a skilled entry level welder. There is an increasing demand for welders in a variety of industries including light and heavy construction, automobile, aircraft, gas and oil, railroad, machinery and manufacturing industries. These skills are developed through theory and hands-on application into various welding specialties including Blueprint Reading and Advanced Computer Aided Design, Oxy-Fuel Welding and Related Processes, Basic Shielded Metal Arc Welding, Basic Gas Metal Arc Welding, and Basic Gas Tungsten Arc Welding. Students learn to use hand-welding or flame-cutting equipment to weld or join metal components or to fill holes, indentations, or seams of fabricated metal products.
Students find employment in industries related to construction, machinery, manufacturing oil and gas, and transportation. Graduates with entry level certifications will find challenging jobs with opportunity for rapid advancement.
What you’ll learn
- Interpret welding blueprints
- Cut and Weld carbon steel using the Oxy-Fuel torch
- Weld carbon steel with the shielded metal arc welding process
- Weld carbon steel, aluminum and stainless steel with the gas metal arc welding process
- Weld carbon steel, aluminum and stainless steel with the gas tungsten arc welding process
Sample Job Titles
Aluminum Welder, Fabrication Welder, Fabricator, Fitter/Welder, Maintenance Welder, MIG Welder (Metal Inert Gas Welder), Sub Arc Operator, Welder, Welder-Fitter, Welder/Fabricator
Soar Agreements
This program enables students to apply certain credits earned in high school to the credits needed for a degree or certificate through Thaddeus Stevens College. The Welding Technology qualifies for this program – see our SOAR program page for details!
Quick facts
Location
Thaddeus Stevens College at Greenfield
Type of program
Associate Degree
Job/Salary Outlook
See industry data
Length of program
2 years, 66 credits
Cost of program
$4,500/semester tuition
$3,000 – $3,500/semester housing
$1,850 – $2,335/semester meal plan
Tool List (PDF)
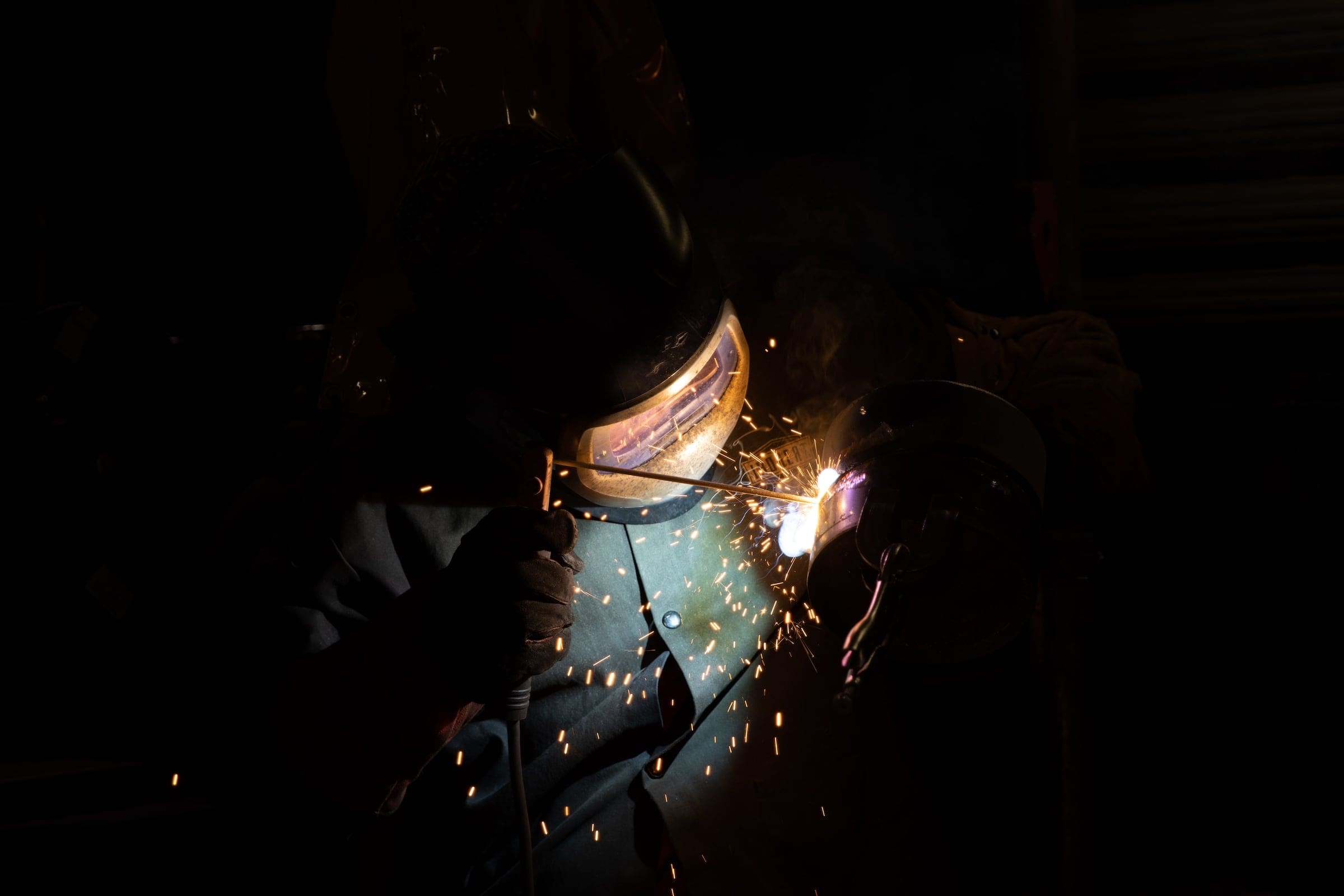
The outcomes speak for themselves
A variety of industries need welders, including light and heavy construction, automotive, aircraft, railroad, and manufacturing industries.
92.6%
employment
$52.5K
med. salary
100%
satisfaction
Program details
Courses
MODEL SCHEDULE FOR WELDING TECHNOLOGY
Semester 1
- WELD 106 Welding Blueprint Reading (4 credits)
- WELD 110 OxyFuel welding and Related Processes (3 credits)
- WELD 121 Shielded Metal Arc Welding (4 credits)
- WELD 150 Introduction to Safety (1 credit)
- MATH 126 Technical Math I (or higher) (3 credits)
- Science Elective (3 credits)
Semester 2
- WELD 155 Gas Metal Arc Welding I (1st 8 wks) (3 credits)
- WELD 160 Gas Metal Arc Welding II (2nd 8 wks) (3 credits)
- WELD 165 Gas Tungsten Arc Welding I (1st 8 wks) (3 credits)
- WELD 170 Gas Tungsten Arc Welding II (2nd 8 wks) (3 credits)
- MATH 136 Technical Math II (or higher) (3 credits)
- ENG 106 English Composition (3 credits)
Semester 3
- WELD 205 Flux Cored Arc Welding (3 credits)
- WELD 220 Shielded Metal Arc Welding II (3 credits)
- WELD 225 Metallurgy (3 credits)
- WELD 230 Special Welding Processes (3 credits)
- Humanities Elective (3 credits)
- HEAL Elective 106 or 111 (1 credit)
- ENG 216 Technical Report Writing (3 credits)
Semester 4
- WELD 260 Gas Metal Arc Welding III (3 credits)
- WELD 270 Gas Tungsten Arc Welding III (3 credits)
- WELD 275 Pipe Welding (3 credits)
- WELD 280 Non-Destructive Testing (3 credits)
- CIS 105 Drawing with Auto CAD (3 credits)
- General Studies Elective (3 credits)
Total Credits 73
Faculty
Occupational Advisory Committee
The Occupational Advisory Committee (OAC) serves as a vital link between the Program of study and industry, ensuring that the program remains aligned with current workforce needs, technological advancements, and best practices in the field. Composed of employers, educators, and other community members, the committee provides guidance, feedback, and recommendations to enhance the curriculum, instructional methods, and student learning experiences.
Purpose and Responsibilities:
- Curriculum & Industry Alignment
- Workforce Readiness
- Student & Faculty Support
- Internship & Employment Connections
- Accreditation & Program Evaluation
- Facilities & Equipment Recommendations
By fostering a strong relationship between academia and industry, the OAC helps ensure that Thaddeus Stevens College programs maintain the highest standards in CTE (career and technical education).
- Yolanda Anderson, Ladder Tower
- Diannia Armolt, American Hydro
- Greg Esh, Goodhart Sons
- Daniel, Feeser, Johnson Controls Navy System
- John Forwood, SWF Industrial
- Cameron Leakey, Goodhart Sons
- Melissa Martin, Viocity Group
- Roch Minnich, Scenic Ridge
- Perry Patton, Walton & Company
- John Peiffer, High Industries
- Sasa Randjelovic, JGM Fabricators & Constructors, LLC
- Jason Smith, BlueScope Buildings North America
- Dave Watson, The Lincoln Electric Company
- Sasha Wawizyniale, Viocity Group
- Gregory Weitzel, High Steel Structures LLC
- Eddie Woodard, ITW/Miller Electric
- Sasa Randjelovic, JGM Fabricators & Constructors, LLC
Essential Skills Learned
Tasks
- Weld components in flat, vertical, horizontal or overhead positions.
- Operate safety equipment and use safe work habits.
- Layout, position, align, and secure parts and assemblies prior to assembly, using straightedges, combination squares, calipers, and rulers.
- Examine workpieces for defects and measure workpieces with straightedges or templates to ensure conformance with specifications.
- Recognize, set up, and operate hand and power tools common to the welding trade.
Tools used in this occupation
- Drill press or radial drill— Drill presses; Portable magnetic drill presses; Punch presses
- Gas welding or brazing or cutting apparatus— Oxyacetylene welding equipment
- Tungsten inert gas welding machine— Heliarc welding equipment; Tungsten inert gas TIG welding equipment
Technology used in this occupation
- Computer-aided design CAD software — Autodesk AutoCAD software; Parametric Technology Pro/ENGINEER software; UGS NX; XY Soft Sheet Cutting Suite
- Computer-aided manufacturing CAM software — Applied Production ProFab; JETCAM Expert; Striker Systems SS-Profile; WiCAM PN4000
- Database user interface and query software — Data entry software
- Spreadsheet software
Knowledge
- Production and Processing— Knowledge of raw materials, production processes, quality control, costs, and other techniques for maximizing the effective manufacture and distribution of goods.
- Design— Knowledge of design techniques, tools, and principles involved in the production of precision technical plans, blueprints, drawings, and models.
- Administration and Management— Knowledge of business and management principles involved in strategic planning, resource allocation, human resources modeling, leadership technique, production methods, and coordination of people and resources.
- Mechanical— Knowledge of machines and tools, including their designs, uses, repair, and maintenance.
- Mathematics— Knowledge of arithmetic, algebra, geometry, calculus, statistics, and their applications.
- Customer and Personal Service— Knowledge of principles and processes for providing customer and personal services. This includes customer needs assessment, meeting quality standards for services, and evaluation of customer satisfaction.
- English Language— Knowledge of the structure and content of the English language including the meaning and spelling of words, rules of composition, and grammar.
- Engineering and Technology— Knowledge of the practical application of engineering science and technology. This includes applying principles, techniques, procedures, and equipment to the design and production of various goods and services.
Skills
- Critical Thinking— Using logic and reasoning to identify the strengths and weaknesses of alternative solutions, conclusions, or approaches to problems.
- Operation and Control— Controlling operations of equipment or systems.
- Monitoring— Monitoring/Assessing performance of yourself, other individuals, or organizations to make improvements or take corrective action.
- Reading Comprehension— Understanding written sentences and paragraphs in work-related documents.
Abilities
- Arm-Hand Steadiness— The ability to keep your hand and arm steady while moving your arm or while holding your arm and hand in one position.
- Near Vision— The ability to see details at close range (within a few feet of the observer).
- Control Precision— The ability to quickly and repeatedly adjust the controls of a machine or a vehicle to exact positions.
- Multilimb Coordination— The ability to coordinate two or more limbs (for example, two arms, two legs, or one leg and one arm) while sitting, standing, or lying down. It does not involve performing the activities while the whole body is in motion.
- Problem Sensitivity— The ability to tell when something is wrong or is likely to go wrong. It does not involve solving the problem, only recognizing there is a problem.
- Visualization— The ability to imagine how something will look after it is moved around or when its parts are moved or rearranged.
- Manual Dexterity— The ability to quickly move your hand, your hand together with your arm, or your two hands to grasp, manipulate, or assemble objects.
- Depth Perception— The ability to judge which of several objects is closer or farther away from you, or to judge the distance between you and an object.
- Information Ordering— The ability to arrange things or actions in a certain order or pattern according to a specific rule or set of rules (e.g., patterns of numbers, letters, words, pictures, mathematical operations).
- Selective Attention— The ability to concentrate on a task over a period of time without being distracted.
Work Activities
- Controlling Machines and Processes— Using either control mechanisms or direct physical activity to operate machines or processes (not including computers or vehicles).
- Handling and Moving Objects— Using hands and arms in handling, installing, positioning, and moving materials, and manipulating things.
- Identifying Objects, Actions, and Events— Identifying information by categorizing, estimating, recognizing differences or similarities, and detecting changes in circumstances or events.
- Operating Vehicles, Mechanized Devices, or Equipment— Running, maneuvering, navigating, or driving vehicles or mechanized equipment, such as forklifts, passenger vehicles, aircraft, or watercraft.
- Communicating with Supervisors, Peers, or Subordinates— Providing information to supervisors, co-workers, and subordinates by telephone, in written form, e-mail, or in person.
- Getting Information— Observing, receiving, and otherwise obtaining information from all relevant sources.
- Performing General Physical Activities— Performing physical activities that require considerable use of your arms and legs and moving your whole body, such as climbing, lifting, balancing, walking, stooping, and handling of materials.
- Inspecting Equipment, Structures, or Material— Inspecting equipment, structures, or materials to identify the cause of errors or other problems or defects.
- Thinking Creatively— Developing, designing, or creating new applications, ideas, relationships, systems, or products, including artistic contributions.
- Training and Teaching Others— Identifying the educational needs of others, developing formal educational or training programs or classes, and teaching.
Work Context
Face-to-Face Discussions – How often do you have to have face-to-face discussions with individuals or teams in this job?
- Wear Common Protective or Safety Equipment such as Safety Shoes, Glasses, Gloves, Hearing Protection, Hard Hats, or Life Jackets— 100% responded “Every day.”
- Spend Time Using Your Hands to Handle, Control, or Feel Objects, Tools, or Controls— 62% responded “Continually or almost continually.”
- Importance of Being Exact or Accurate— 56% responded “Extremely important.”
- Face-to-Face Discussions— 73% responded “Every day.”
- Exposed to Contaminants— 60% responded “Every day.”
- Indoors, Not Environmentally Controlled— 71% responded “Every day.”
- Frequency of Decision Making— 59% responded “Every day.”
- Work With Work Group or Team— 43% responded “Extremely important.”
- Impact of Decisions on Co-workers or Company Results— 43% responded “Very important results.”
- Structured versus Unstructured Work— 45% responded “A lot of freedom.”
- Time Pressure— 44% responded “Every day.”
Interests
- Realistic— Realistic occupations frequently involve work activities that include practical, hands-on problems, and solutions. They often deal with plants, animals, and real-world materials like wood, tools, and machinery. Many of the occupations require working outside and do not involve a lot of paperwork or working closely with others.
- Conventional— Conventional occupations frequently involve following set procedures and routines. These occupations can include working with data and details more than with ideas. Usually, there is a clear line of authority to follow.
Work Styles
- Attention to Detail— Job requires being careful about detail and thorough in completing work tasks.
- Dependability— Job requires being reliable, responsible, and dependable, and fulfilling obligations.
- Adaptability/Flexibility— Job requires being open to change (positive or negative) and to considerable variety in the workplace.
- Independence— Job requires developing one’s own ways of doing things, guiding oneself with little or no supervision, and depending on oneself to get things done.
- Innovation— Job requires creativity and alternative thinking to develop new ideas for and answers to work-related problems.
- Integrity— Job requires being honest and ethical.
- Leadership— Job requires a willingness to lead, take charge, and offer opinions and direction.
- Analytical Thinking— Job requires analyzing information and using logic to address work-related issues and problems.
- Initiative— Job requires a willingness to take on responsibilities and challenges.
Work Values
- Support— Occupations that satisfy this work value offer supportive management that stands behind employees. Corresponding needs are Company Policies, Supervision: Human Relations, and Supervision: Technical.
- Working Conditions— Occupations that satisfy this work value offer job security and good working conditions. Corresponding needs are Activity, Compensation, Independence, Security, Variety, and Working Conditions.
- Relationships— Occupations that satisfy this work value allow employees to provide service to others and work with co-workers in a friendly non-competitive environment. Corresponding needs are Co-workers, Moral Values, and Social Service.
Performance Measures
Internal Key Performance Indicators (Sources: Internal data collections, and Post-Graduate Surveys)
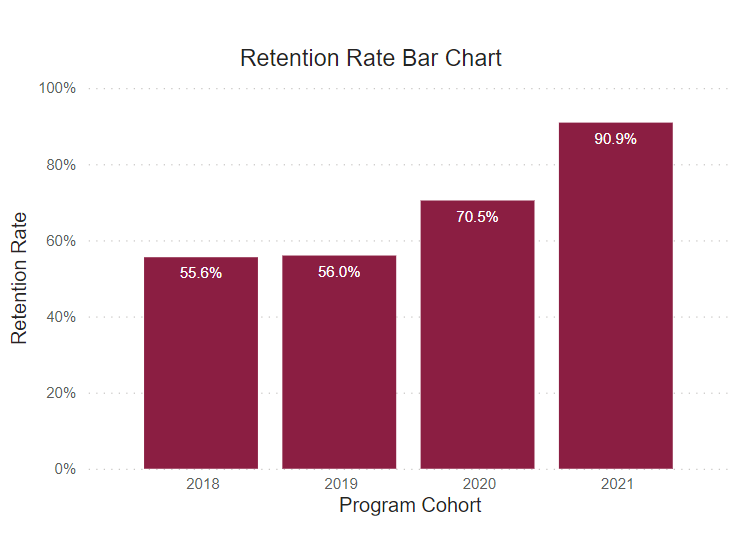
Retention Rate
This rate reflects the continuous term-to-term persistence rate for certificate programs and the fall-to-fall retention rate for associate degree programs.
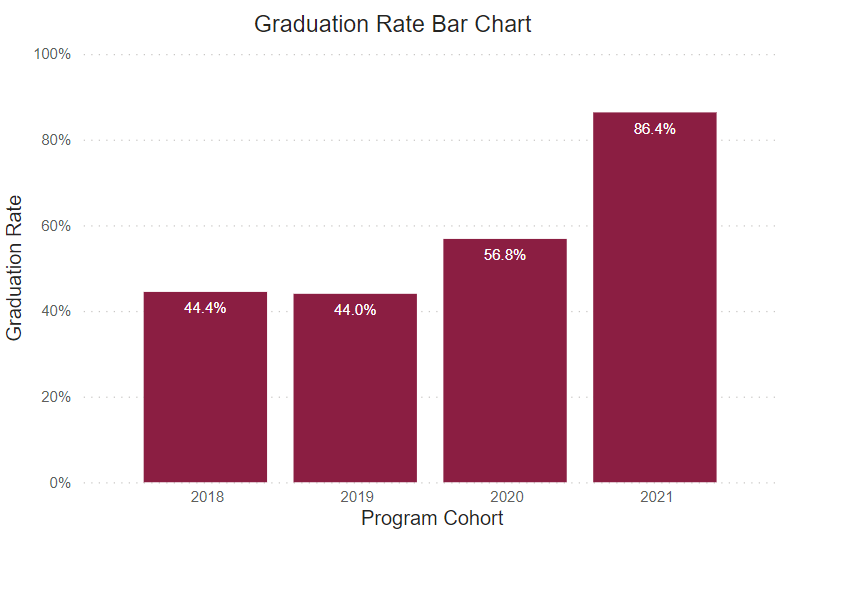
Graduation Rate
This rate reflects the number of freshmen who were officially enrolled in the fall semester and earned a certificate or degree within the expected timeframe.
Post Graduate Survey Response Rate
The post graduate survey is an annual on-line post graduate survey utilized by the college to gather vital information regarding career placement, starting salary, and level of satisfaction.
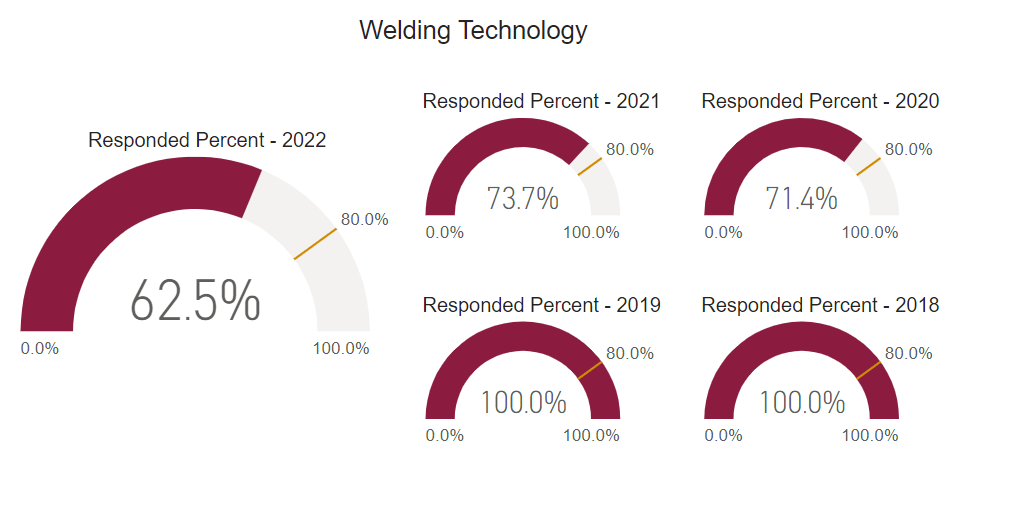
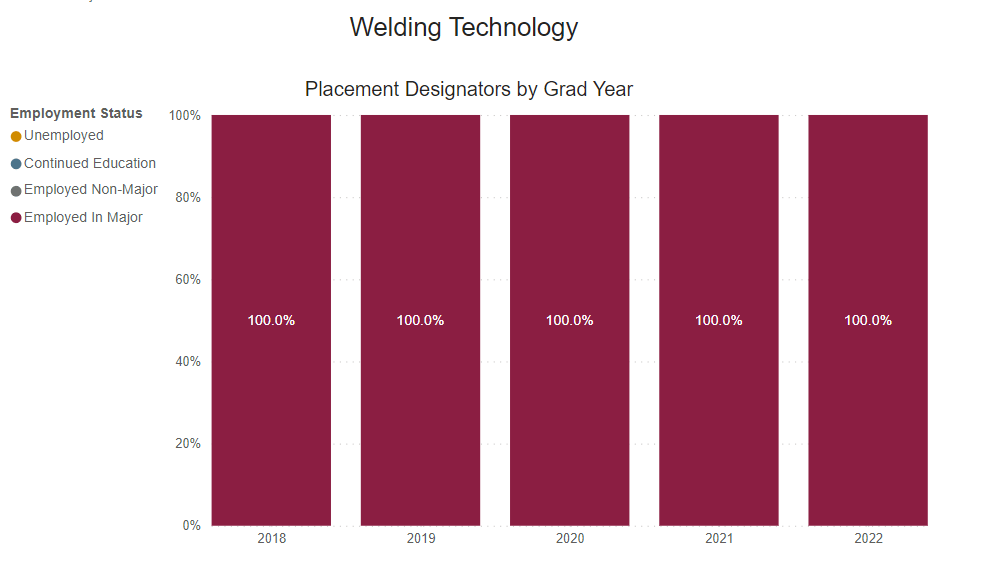
Employed Full Time Outside of Major
Percentage of graduates who reported being employed full-time outside their field of study.
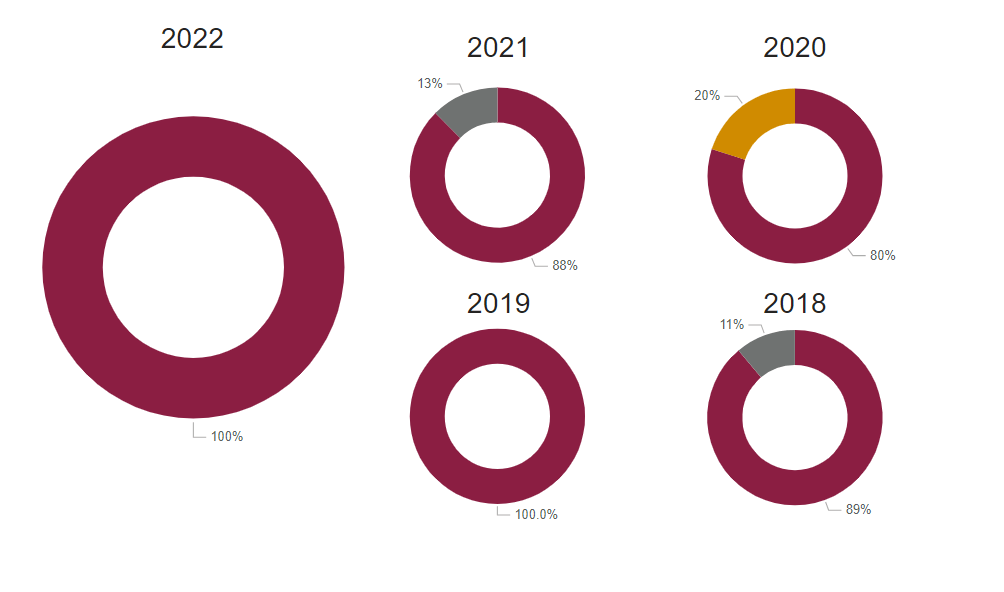
Graduate Satisfaction
This is the median graduate survey response evaluating the level of preparation for workforce entry (based on a 5-Item Likert Scale).
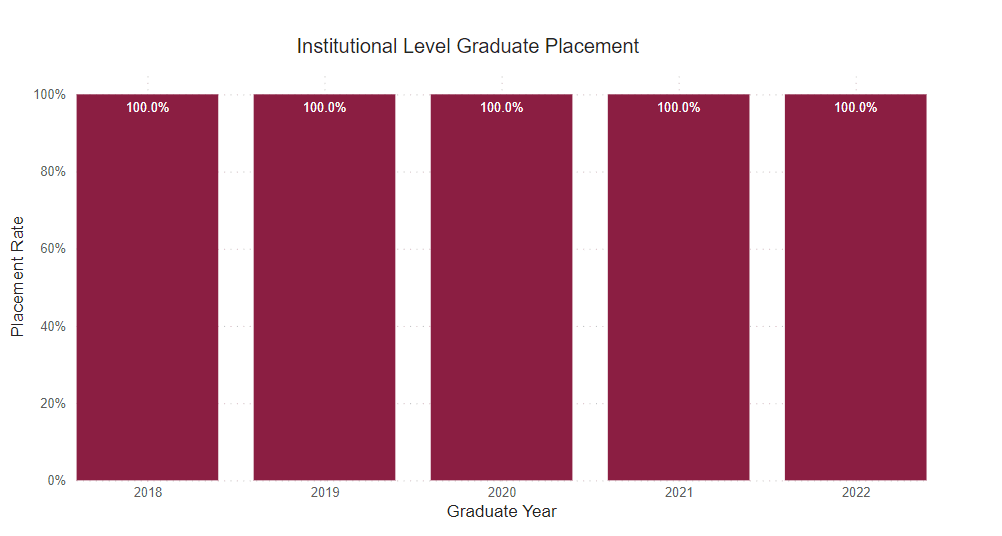
Placement Rate
This is the percent of graduate survey respondents who reported being employed or continued their education on a full-time basis.
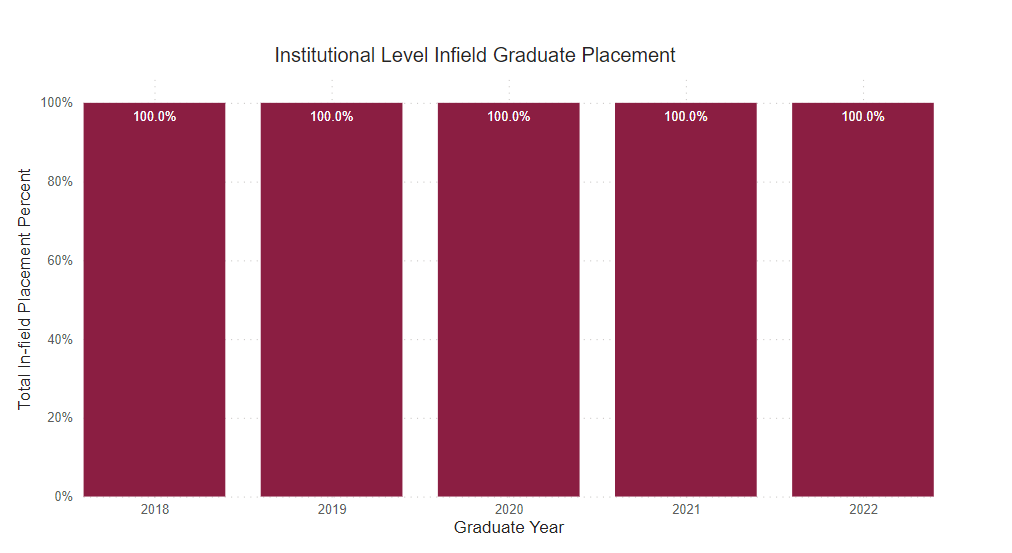
Employed Full Time Within Major
Percentage of graduates who reported being employed full-time within their field of study.
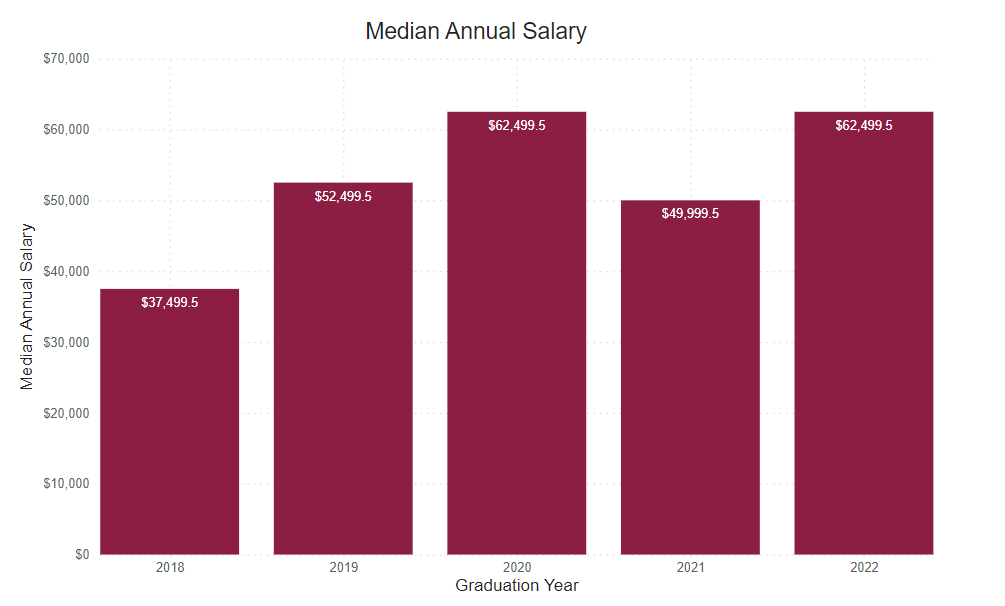
Annual Median Starting Salary
This number is based on the graduate survey response to the request to identify a starting salary from a range of options. This graph shows the median first-year annual salary. All calculations are based on the respondent’s self-reported first-year annual income.
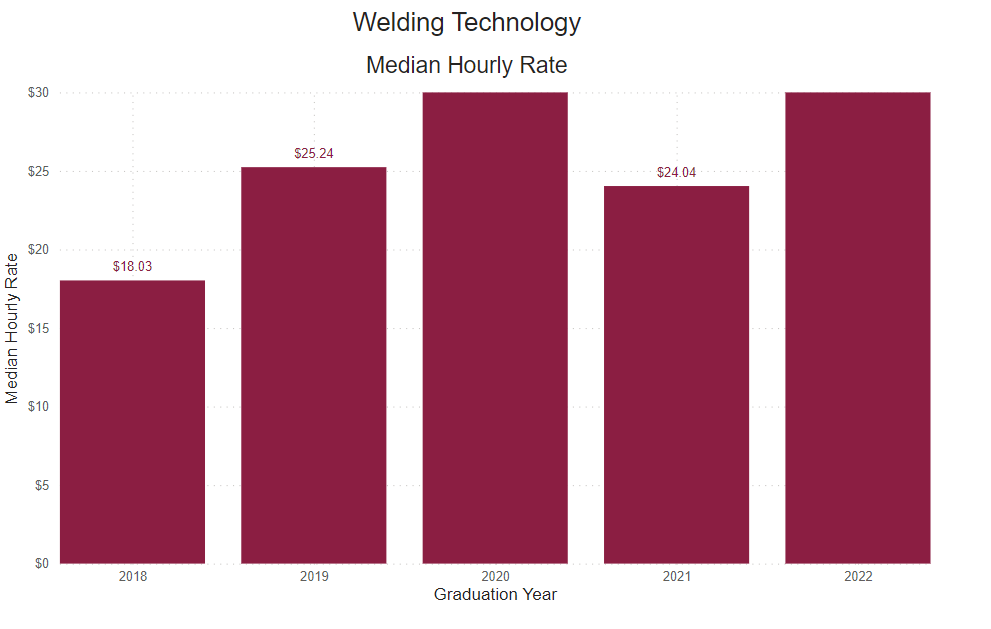
Reported Hourly Rate
This number is determined by dividing the reported median salary by the number of hours in a traditional full-time work week (40), then the number of weeks in a year (52).
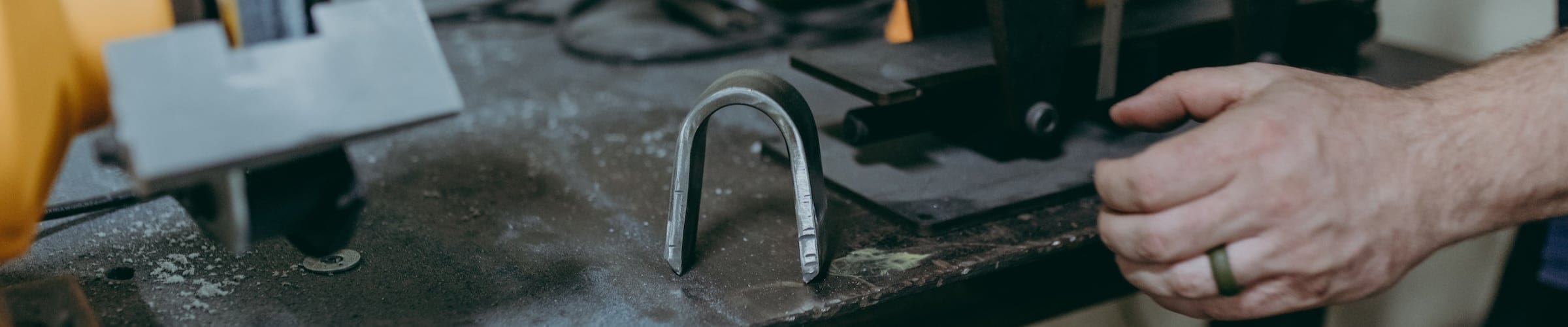
Our graduates work with the industry’s best